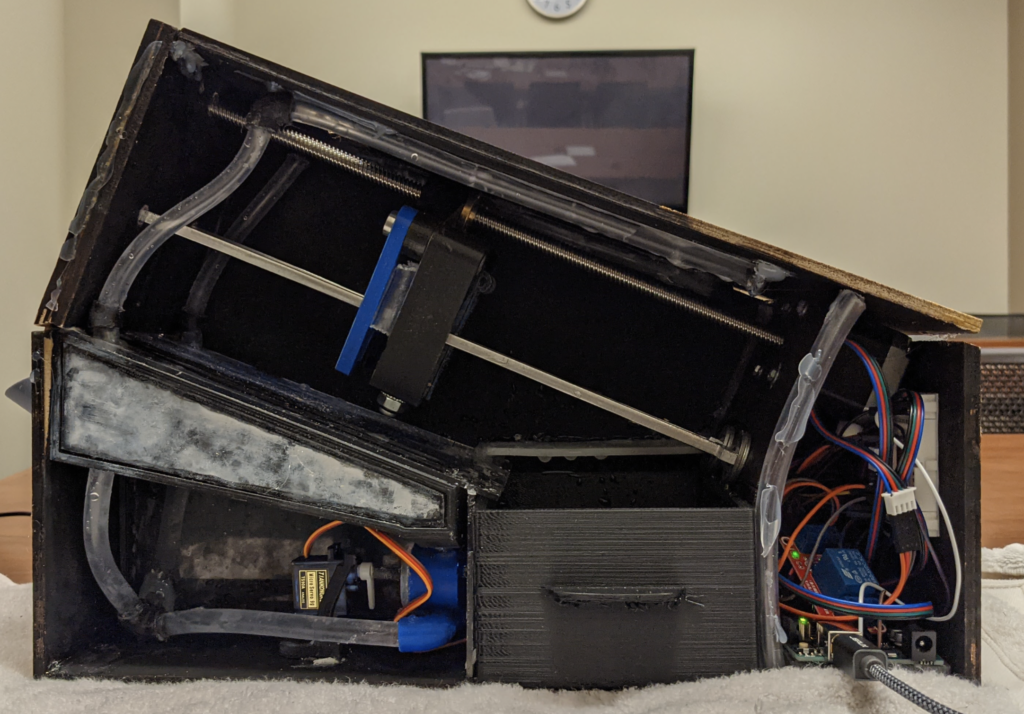
Our final Theseus Knife Cleaner Prototype
Overview:
Sophomores in Purdue ME take ME 263, a sophomore design class. It is a class designed to teach students about the fundamentals of problem scoping, meeting customer requirements, and building a rudimentary prototype.
I knew from the start that I wanted our team (Team Theseus) to do something more challenging than that, both for our own interest, and so that we could get some hands-on experience out of the whole process.
In the end, we spent many late nights designing, manufacturing, and testing a prototype that was, frankly, overengineered. Still, we got invaluable experience working with liquids, waterproof materials, microcontrollers, electronics, and new manufacturing tools.
Our design also won the ‘Best Design’ award for our ME 263 section, awarded by industry panelists
Part I: The Problem
At the beginning of the process, we decided we wanted to invent a way to automatically clean knives quickly, safely, and easily, to eliminate one of the more annoying parts of the cooking process.
We were able to break this goal down into a number of subfunctions we wanted to achieve:

Functional Decomposition Chart of Knife Cleaner
Part II: The Design
After defining the problem and our goals for the product, we had to design ways to achieve those goals. We started this by creating concept drawings of different mechanisms before choosing the best ones and converting them into a 3D model of our final product.

Final concept drawing of full system including carriage, fluids, and control system subassemblies
The product sprays the knife with soap and water, scrub the knife, and dry the knife. To do this, it has a pump system as well as a ‘soap carburetor’ to mix soap into water and spray the knife with it. Then a carriage attached to a stepper motor. This pulls a sponge and a squeegee that squeezes the knife as it moves. This scrubs and dries the blade. The design also features refillable soap and water tanks within the machine.

Full Assembly Design in Fusion360
Part III: Manufacturing and Assembly
This part of the process was by far the most fun. For around 3 weeks, I spent many late nights, often alone, in the workspace of the Purdue ME building, assembling and testing the electrical systems of the device, manufacturing the individual components, and finally integrating them all into the final product.
Overview of fluids tank subassembly

Final electrical assembly, connected to carriage stepper motor, carburetor servo, and pump relay
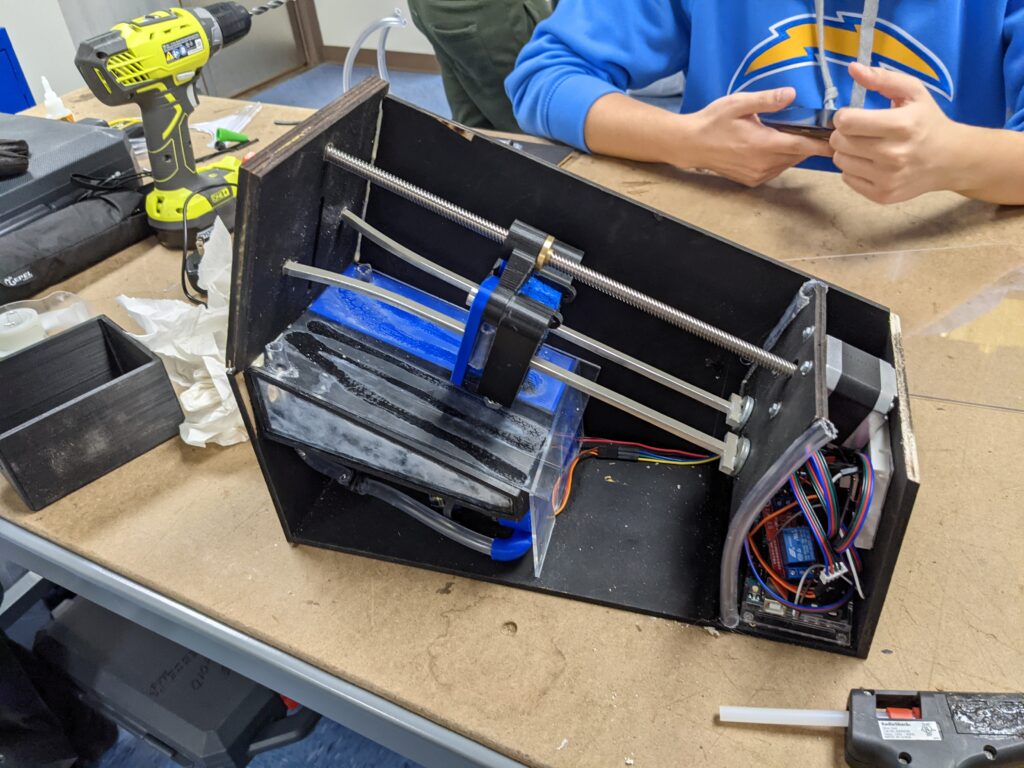
Prototype with full carriage assembly installed
Part IV: Finished Prototype
Did our prototype do what we wanted it to? Not quite. We wanted it to be able to actually clean a knife that we could give it, but due to a number of problems with the design- excess friction on the carriage, the soap carburetor being too small to be assemblable, and general lack of waterproofing – seriously limited what we were willing to attempt.
In the end, our design proved our concept in some ways while also proving just how overcomplicated our design was. Looking back, a simple design similar to a knife block made out of a reinforced sponge material would have allowed for very convenient knife cleaning by insertion/removal from the block.
But, despite challenges and limitations of our prototype, this project was a remarkable success in terms of my own growth as an engineer. I got to work with components and mechanisms I had never worked with before, learned tough lessons about designing for manufacturing and assembly the hard way, and had a blast getting to work hands-on on a project of my own choosing.