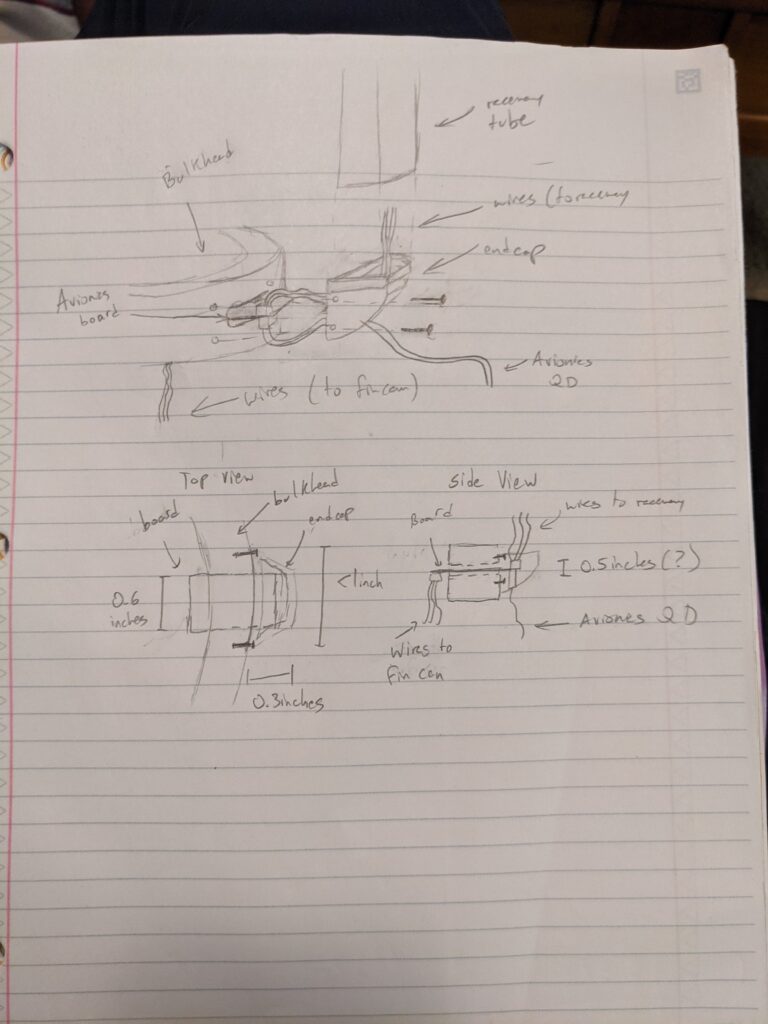
Overview
The Purdue Space Program Liquids team are some of the brightest, most amazing engineers I’ve ever met. They design, build, and test liquid rockets (an extremely hard challenge to do at the scales they do it at) from scratch to compete in the FAR MARS competition.
I originally joined the structures team to work on a ‘knitting’ project (described below) but am currently doing work on sensors that will help retrieve flight and structural data on the CraterMaker Special, their next liquid rocket.
CraterMaker Special
CraterMaker Special (CMS) is PSP Liquid’s next, biggest liquid rocket, currently in early planning and design in fall of 2022. I am working with the structures team to try and design an array of sensors to monitor flight stresses- forces from parachutes, torsional forces, and fin flutter – so that the structures team can design parts as well as possible.
Sensors
I’ve done both research and development with sensors. To make strain gauges do what we want them to, I’ve learned a lot about them and tried to make some from graphene.
I compiled my research into strain gauges into one easy-to-read document for reference to other members of the structures team. Read it below.
We also were able to print graphene into desired patterns using Kapton tape and a laser engraver. The next step is to test the resistance of these tests and see if they can be accurately used as strain gauges.
Knitting
One of the most important parts of liquid rockets are highly pressurized tanks that hold things like liquid oxygen at cryogenic temperatures. To do this, rockets are build with COPVs (Compression Over-wrapped Pressure Vessels). COPVs are extremely strong tanks made of metal but wrapped in a composite material like carbon fiber. This use of materials allows them to hold extremely high pressure while remaining light enough to put on a rocket.
COPVs are expensive and often hard to procure, so PSP Liquids decided to pursue building a ‘knitting’ machine- a computer-controlled device that would wrap composite filament around a metal tube. I got involved because I was interested in the math and programming that would go into such a problem.
We began by reading a lot of the theory behind filament winder machine software: path generation techniques for different tube geometries, equations that govern winding angle and the biggest challenge: how to wrap the round ends of a tank.
We started actual work by graphing what basic toolpaths could look like on the simplest mandrel shape there was: a cylinder.

One of our graphs of possible winding paths for a cylinder mandrel. The hard parts of this were finding ways to wrap the corners while leaving space for a central axle as well as making sure that fibers were spaced in such a way that they tiled the entire surface area of the mandrel instead of stacking on top of each other.
Knitting was a really fun math, CS, and engineering challenge, but due to changes in PSP’s priorities, it was unfortunately cancelled before we were able to really go anywhere with it.