
The final Line Wrangler Poster presented in our senior design showcase
All Purdue Mechanical Engineering students take ME 463, our senior design capstone. As a California native, I wanted to pick a project that could use engineering to help decrease the destruction caused by wildfires, an all-too-common reality in 2024.
I soon learned that power line failures cause a disproportionate amount of wildfire damage in the country each year, and usually the only thing protecting us from line failures are visual inspections.
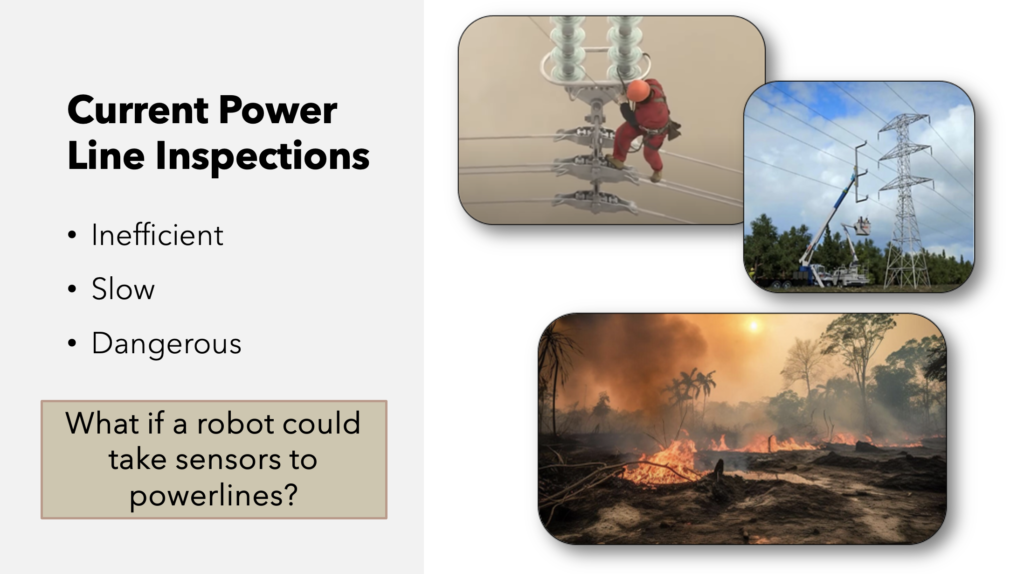
Sensors exist to measure temperature, conductor quality, line sag, and other data that can predict failure. The missing piece is getting sensors to power lines. For our semester-long project, we limited our scope to this physical traversal aspect of inspection robots.

We spent a lot of time researching existing Power Transmission Line Inspection Robots (PTLIRs) and developed an architecture that would allow us stability and flexibility
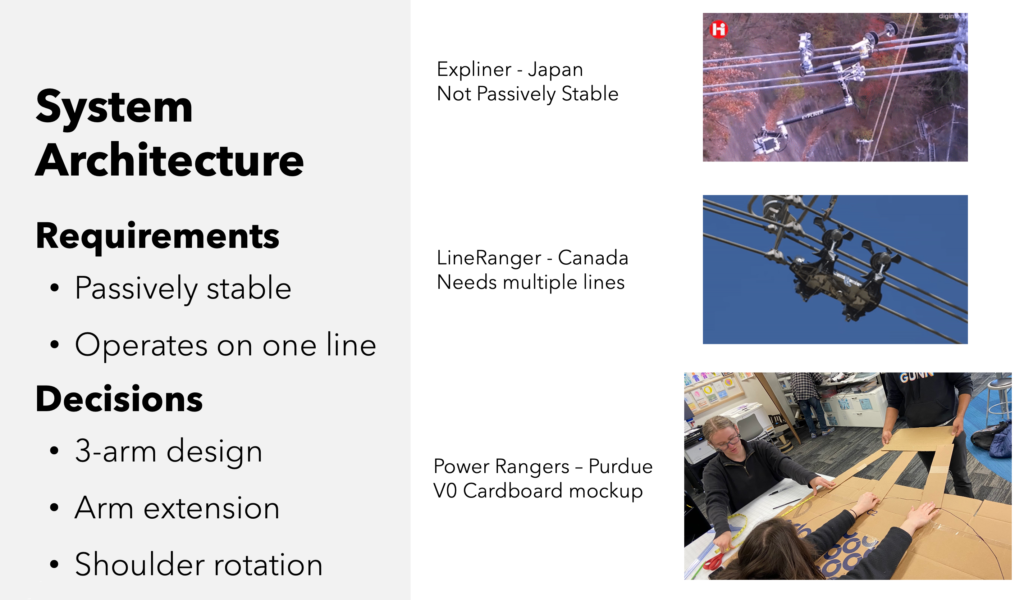
The design centers on a chassis suspended by 3 arms, each of which can extend and rotate in two directions. The extension and rotation of each arm works by using a linear actuator that pushes a pin in a track, which guides extension and rotation
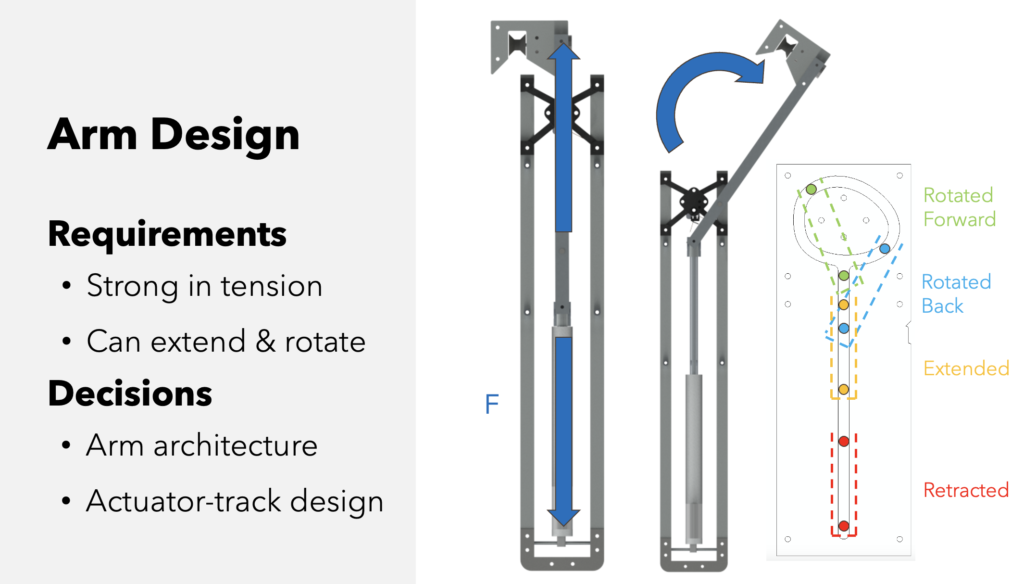
Each arm can rotate along a second axis thanks to another “shoulder” actuator. This second axis of rotation allows for better avoidance of obstacles located on a cable by allowing for arms to move along the cable at a distance.

The chassis itself is designed to be passively stable and rigid, making the entire structure of the device as sturdy as possible.
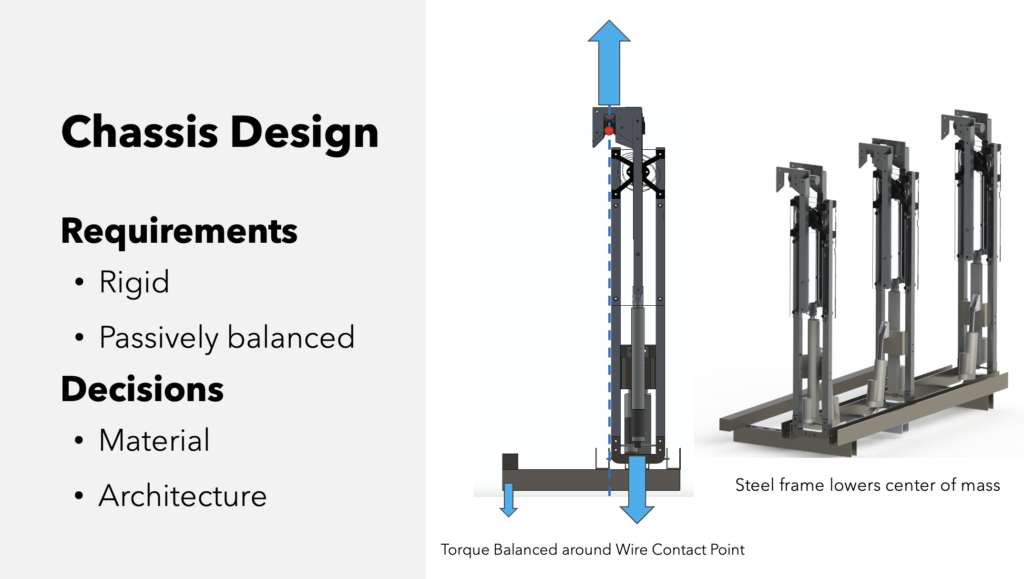
Our final product is tele-operated, and requires a human to guide the path and commands of the robot as it moves. Future designs will improve on the device’s strength, flexibility, and autonomy, and allow for better traversal of even more representative power line testing architectures.